Fabricating Optimized Shields for COVID-19 First Responders
May 16, 2020
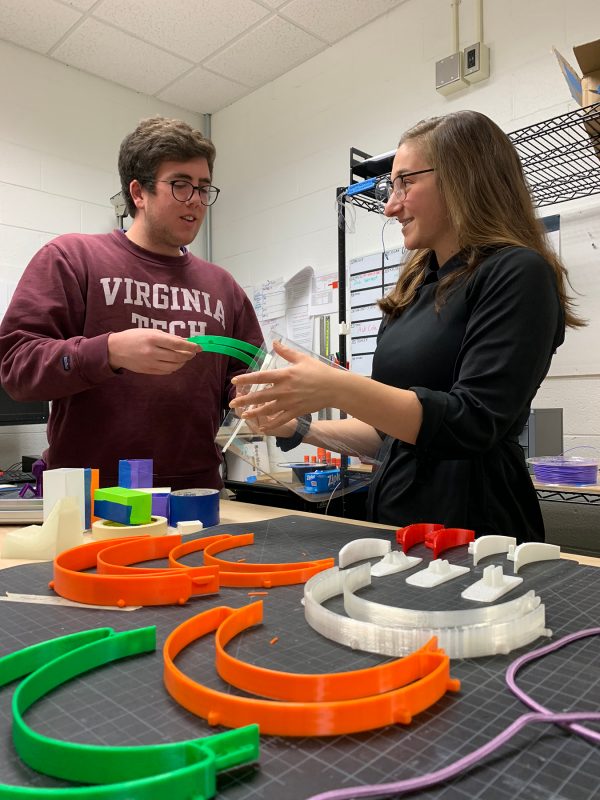
Cole Powell, 4th-year industrial design, and Gabriella Perry, 5th-year architecture, examine 3 D printed prototype for COVID 19 face shield.
A team from the School of Architecture + Design’s Center for Design Research is providing shields for hospital workers and first responders.
As the need for face shields continues with the spread of the COVID 19, Mark Leach, shop supervisor and Jonathan Rugh, lab craftsman, considered how their skills and capabilities could be deployed. Jon first raised the question, and Mark’s spouse, Patty Kitchin, a physician at Centra Lynchburg General Hospital, validated the need. She sounded the alert that there would be need for personal protection equipment at smaller hospitals that do not have the procurement possibilities of the larger facilities. It soon became clear the same problem was situated with many of the local first responders and emergency crews.
Considering speed, efficiency, cost and durability as criteria for design thinking, they first established priorities with respect to specific needs. Given the circumstances of the national health emergency, they determined speed and efficiency of fabrication were critical as long as the ergonomic fit of the shield for health care workers was fulfilled.
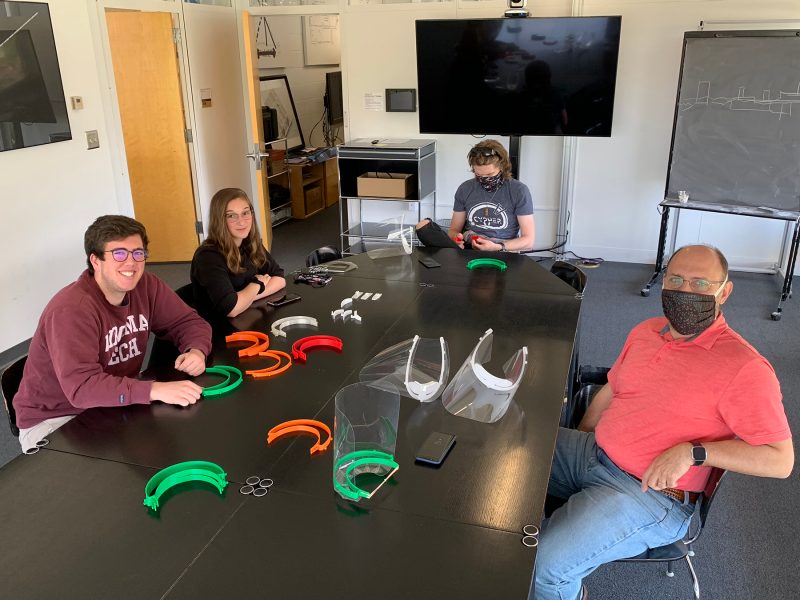
Cole Powell and Gabriella Perry of the Center for Design Research in the School of Architecture + Design and Alexander Leonessa and Liam Chapin of the Terrestrial Robotics Engineering & Controls Lab discuss design optimization of COVID 19 face shields.
Working through the School of Architecture + Design’s Center for Design Research, they studied many of the open-source designs available on the internet. Each was found to have its own particular strengths and weaknesses, ranging from speed of production but lacking in comfort, to fully operational but time-consuming in fabrication and unnecessary use of material. They set out to optimize a design. The CDR provided initial funding for the project and Home Depot in Christiansburg generously donated sheets of Plexiglas to increase production capacity.
Having both laser cutting and 3-D printing technologies available, they first focused on the former. 3-D printing has the attributes of precise complex forms, but its scalability is compromised by long production times and heavy use of material. The search for fast fabrication in conjunction with high unit quantity directed the design towards laser cutting. Modifying an internet available prototype, they arrived at a light gauge plexiglass frame in which 24 can be cut in an hour. A thin sheet of plastic attached to the frame is also laser cut as is a small insert offering overhead protection. Thus far, 200 shields have been delivered to local agencies such as Blacksburg Rescue, Christiansburg Rescue, Montgomery County Department of Social Services, Lynchburg Centra General Hospital, Floyd, Franklyn, and Botetourt Rescue, Giles Co Rescue, a medical office in Martinsville, and VCU Critical Care Transport.
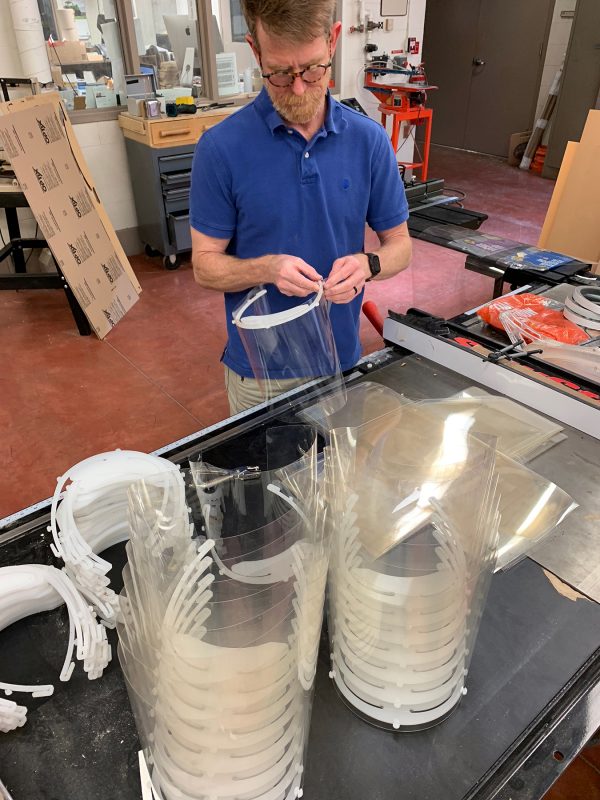
Mark Leach, member of the Center for Design Research and shop supervisor inspects laser cut face shields.
In conjunction with the shield development, two undergraduate students, Gabriella Perry, fifth-year architecture and Cole Powell, fourth-year industrial design, studied further the viability of 3-D printing. Working in the CDR Additive Manufacturing and Prototyping lab (AMP), they first studied the ergonomics (fit and comfort) of the laser cut version and designed a small insert attachment that would better sit on the forehead of the user. The printing time is minimal, making the additional part a viable alternative. They also examined ways to optimize a full printed version of the frame. Working with another open-source 3-D printed prototype, they were able to cut the printing time and material use in half, thus doubling production capability.
The work is ongoing, depending on local and regional need. It is a small contribution, to what is a national and global emergency, in the spirit of service integrating teaching, learning and research.